Replacement Windows Massachusetts can improve the look of your home and add resale value. They can also lower your energy bills and prevent future damage to the frame.
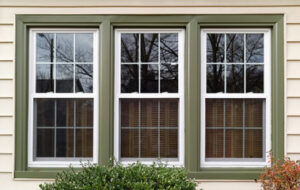
Today’s new window options include styles with blinds tucked between the glass that eliminates the need for dusting and makes cleaning easier. They can also quiet outside commotion to help you relax and sleep better.
If you are replacing windows in your home you will have to decide what style to choose based on a variety of factors including exposure and the look you want. There are two main types of installation: full-frame and pocket. Full-frame installations require removing the old window and installing new framing to accommodate your replacement. These are referred to as new construction windows and typically have nail fins on the edges of the frame to allow them to be fastened directly to your house’s studs.
Pocket installations utilize the existing frame and are slid into place by professional window contractors. These are referred to as replacement windows and can be either flush fin or block-fin. If you have a stucco or block wall and are replacing a window with one of these styles you will want to select a flush fin window that has a sloped sill adapter, which allows the new window to fit into the existing wood sloped sill of your home’s exterior.
You can also use a flush fin window in a stucco wall with the proper flashing details. You may need to install a sloped sill adapter and add some caulking at the bottom of the frame to create an air and water barrier between your new window and the building.
Another thing to consider is the condition of your existing frame. If your frame is in poor condition you will need to use a full-frame replacement window and not a pocket style. If you are installing a new window that is the same size as the old one then a pocket window will be fine.
Another option is to use a full-frame replacement window without a nail fin. This is more common in older homes with siding or stucco and allows you to match your replacement window exactly with the existing frame. However, this type of installation has created enough leak problems in the past that some jurisdictions now require permits to be pulled for the installation and you must have a skilled window installer to make sure your replacement windows are flashed properly.
Insert
When it comes to installing new windows, homeowners have two options: insert windows and full frame replacement. Both installation methods offer advantages and disadvantages, but which one you choose depends on the condition of your current window frames and studs. Learn more about these two installation methods to help you determine the best solution for your home.
Also known as “frame-in-frame” or “pocket window,” insert windows fit within your existing frame and are only used when the exterior cladding, trim and interior of your old windows are still in good shape. This method allows you to preserve the look of your home and upgrade its energy efficiency, durability and overall functionality.
The biggest advantage of this installation method is that it’s much faster and less invasive than replacing the entire frame. Because of this, it’s ideal for older homes with original, solid wood frames that you want to keep.
Another option is block frame windows, which replace the sash only and leave your original frames intact. This installation method is typically done in cases where you’re happy with the size, shape and operating style of your existing windows and when the walls are made from brick or siding.
Like insert windows, they’re installed from the interior and don’t have a nailing fin, but unlike flush fins, block fins extend up the framed wall to help prevent water and air leaks. This feature makes block frame windows an ideal choice for historic and pre-fabricated wall construction, especially in areas with a lot of moisture.
Double-Hung
Double-hung windows are one of the most popular replacement window styles and come in a range of sizes. Their upper and lower sashes slide vertically in separate grooves, making them easily adaptable to most architectural styles. They also allow superior ventilation and control of airflow throughout a home. Cool summer breezes can enter through the bottom sash while hot, stale indoor air can escape through the top sash. This feature is particularly useful in two-story homes and helps improve energy efficiency.
Another advantage of double-hung windows is their ability to be opened from both sides, which allows them to provide better ventilation than other types of replacement windows. This can help reduce harmful fumes from cooking and cleaning, and it’s ideal for those with children in the house. Double-hung windows are also easy to clean. By simply tilting the sashes inward, you can reach even hard-to-reach areas for a thorough cleaning without having to step outside.
On the downside, double-hung windows can be more expensive than single-hung windows. This is because they have more moving parts and are typically built using more complex construction methods. This may lead some homeowners to shy away from these windows, but those who are willing to pay more for increased functionality, a wide range of design options, and better ventilation should be able to find a product they love.
Ultimately, double-hung windows are worth the investment. They are an excellent choice for many different home styles, offer a high level of customization, and can be paired with a variety of frame materials, colors, and finishes to create the look you desire. They also add resale value and can improve your home’s efficiency.
However, if you’re looking for an affordable option that offers the same benefits as double-hung windows, you might want to consider choosing a single-hung window. Single-hung windows are easier to install and do not require as much maintenance or upkeep as double-hung windows. They are also an excellent choice for older homes with outdated windows, which may have lost their argon or krypton seals.
Single-Hung
While single- and double-hung windows are popular options for homeowners looking to replace old windows, the window styles you choose will depend on your home’s needs and space constraints. If you’re looking to increase the size of your window opening, for example, you may want to consider casements or sliding windows as a more appropriate option.
Aside from the aesthetic benefits, double-hung windows offer ventilation and accessibility features that make them ideal for homes with second floors. They also allow you to clean the inside and outside of the sash from either side of your home, which is especially helpful for homeowners with small children or pets.
On the other hand, single-hung windows are more straightforward and less expensive to purchase because they have fewer moving parts. In fact, they’re often used in new home construction because their simple design makes them easy to install and affordable for builders.
Because single-hung windows open only from the bottom, they’re also ideal for areas where an outward-opening window might obstruct pathways or patios. They’re also more energy-efficient than their double-hung counterparts because the movable sash limits air leakage and infiltration.
Another important distinction to keep in mind is that replacement windows are designed for use on existing frames, whereas new construction windows are built for new building projects and have fins that must be attached to the frame. If you’re planning a new build and would like to include windows in the wall frame, new construction windows are the best choice.
Finally, insert windows are similar to new-construction windows, but they’re installed into an existing frame rather than a full wall. They’re typically only used with original solid-wood frames that are in good condition, and they involve pocketing the fully assembled window into a space in the wall. They’re generally used in situations where there are structural or rot concerns that would otherwise prevent new construction windows from being installed.