Frameless Glass Shower Doors are becoming more popular for homeowners looking to upgrade their bathrooms. They offer a sleek, modern look and are easy to clean. They can also add value to your home.
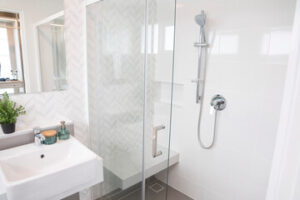
However, they can be more expensive than framed shower doors. Additionally, they can take longer to install than framed doors. This is because frameless shower doors need precise measurements to ensure a perfect fit. Visit https://glassgovernor.com/ to learn more.
A frameless glass shower door is an excellent upgrade for any bathroom. It makes the room feel more spacious and opens it up for more natural light. However, it may cost more to install than a traditional framed shower. The reason is that frameless doors require specialized hardware that isn’t usually sold in home improvement stores. Also, the glass is more expensive because it needs to be tempered and a protective coating applied. Adding this to the total installation cost can increase your budget significantly.
If you want to save money on your frameless shower doors, look for a company that specializes in custom cuts. This will ensure that the glass is precisely cut, reducing the chances of leaks. Then, the installer can caulk around the edges of the glass to seal it. A clear vinyl sweep can be installed at the bottom of the shower for additional leak protection.
You can find a lot of different styles for glass shower doors, including those with a curved track and those with handles or knobs. They are available in a variety of tints, finishes, and coatings to match any style. You can even have a color or pattern added to the glass to make it more unique. Regardless of the style you choose, you should always get a quality door from an experienced, reputable company. Otherwise, you could end up with a costly renovation due to poor workmanship.
Frameless glass shower doors are easier to keep clean than framed ones because they have less nooks and crannies where mold and mildew can grow. However, it’s important to squeegee the doors after each use to prevent soap scum and water spots from forming.
While the cost of a frameless shower can be higher than that of a framed one, you’ll still save money by choosing a simpler design and installing it yourself rather than hiring a contractor. You’ll also avoid paying extra fees for testing and remediation of hazardous materials. In addition, a general contractor’s overhead and markup will add to your overall costs.
Durability
Unlike the metal shower frames that can rust and detract from the appearance of your bathroom, frameless glass showers are a long-lasting and durable option. This is due to the fact that they are typically made from tempered glass, which is up to 10 times stronger than standard annealed glass. Tempered glass is also safer to handle than annealed glass, as it is less likely to break into dangerous shards.
The durability of frameless glass showers is further enhanced by the use of high-quality hardware. This includes hinges and handles, which should be made from corrosion-resistant materials. Additionally, the hardware should be aesthetically appealing and easy to maintain.
Frameless shower doors are easier to clean than framed ones because they have less nooks and crannies that can collect soap scum and mildew. However, they do not eliminate the need to clean your bathroom completely, and it is still important to squeegee after each use to prevent mold and mildew buildup.
In order to prevent water leaks, it is essential that the installer of your new shower uses a silicone caulk along the edges of each fixed panel. This will help to keep water from seeping through the shower doorway when it is closed. In addition, you should ask your contractor to use a thick bead of caulk at the corners of the fixed panels and on the frameless glass enclosure to prevent water from seeping out.
Installing a frameless glass shower is a complex job that is not for the weekend warrior handyman. It is best to leave the installation to a professional, as the slightest mistake can crack or chip your new shower door. This could be expensive and may require replacement of the door.
When choosing a contractor to install your new frameless glass shower, be sure that they are licensed and insured. Also, make sure that they are familiar with the requirements for installing frameless showers in your state, as there are a number of regulations that must be followed to ensure the safety of you and your family. Finally, it is recommended that you choose a contractor with experience installing frameless glass showers. This will give you peace of mind that they know what they are doing and will have the necessary tools to complete the job correctly.
Appearance
Frameless shower doors can add elegance to a bathroom design and improve the flow of natural light. They are also more durable than framed shower doors and require less maintenance. They are also an affordable upgrade for many bathrooms.
These glass doors are available in a wide variety of colors, shapes, and textures. If you are looking for a specific appearance, talk to your design consultant about the possibilities. They can guide you through your options and help you select the best door for your space.
Framed and frameless shower designs differ in their choice of hardware, which can influence the appearance of the glass. While framed shower doors use aluminum trim, frameless enclosures have chrome or nickel trim instead. The trim is usually a square or rectangular shape and can be in either satin or polished finish.
The doors themselves are usually made from tempered glass, which is thicker and more resistant to breakage. Tempered glass is more likely to shatter into small, blunt-edged pieces, which will reduce the risk of injury compared to sharp jagged shards of regular glass. However, even if you have a frameless glass shower, it is important to ensure that the doors are properly installed. Check them regularly for cracks and chips, and never slam the doors.
While it is possible for frameless glass shower doors to shatter, this is rare and usually the result of accidents or sudden changes in temperature or humidity. In addition, the lack of a frame means that shattered glass is unlikely to get into your water supply or cling to you when you bathe or shower.
Because of their minimalistic design, frameless glass shower doors are easier to clean than framed doors. They have fewer nooks and crannies where mold and mildew can hide, and they are easy to wipe down after each shower with a squeegee or sponge.
A frameless glass shower can reveal bathroom tiles that are otherwise hidden by a curtain, which can make the room feel larger and brighter. In addition, the clear glass can show off marble tile or stonework. Adding a bench or knee walls to your frameless shower enclosure can further enhance the appearance of the room.
Installation
If you’re planning to install a frameless shower door in your home, it’s best to have a professional handle the installation. The process is complex and requires many tools and supplies, including a drill, hammer or mallet, caulk gun, and waterproof silicone sealant. Considering that even the slightest mistake can lead to a shattered glass door, it’s not something you want to do on your own.
Before starting the installation, clean the shower opening thoroughly. Remove any existing shower doors and hardware from the wall. You should also make sure the area is dry and free of debris before proceeding. The next step is to assemble the shower hardware kit according to its instructions. Once the kit is assembled, it’s time to install the bottom track and the side jambs. After the tracks and side jambs are in place, you can begin installing the hinges. These can be either regular or pivot hinges, depending on your preference. You should also add a door guide at this point.
Once you’ve completed the installation of the track, side jambs, and hinges, it’s time to add the door. You can choose between a sliding or a bi-fold door. Once you’ve decided on which type of door to get, it’s important to take measurements before ordering the glass panel and ensuring that everything will fit together properly.
Some people are concerned that the lack of a frame makes these showers more likely to break or shatter during normal use. However, this is a very rare occurrence, especially if the doors are properly installed and used. In addition, the shower walls are usually reinforced with fiberglass or another material that is much stronger than glass, making them very resistant to damage.
Frameless showers are also easier to keep clean than their framed counterparts. They have fewer nooks and crannies for mold to grow, and cleaning is as simple as wiping down the doors and glass with a squeegee every day after showering. If you want to save money on installation and maintenance costs, consider using a frameless shower enclosure in your bathroom.