Florida Injection Molding Tooling refers to the metal parts that clamp and close a plastic mold. The tool also includes ejector pins that push finished parts out of the mold once it’s cooled.
Tight tolerances are possible with injection molding, but it requires a thorough design process. Injection mold tooling is one of the longest lead-time items in a project.
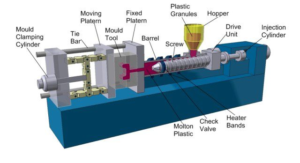
Injection mold tooling shapes the final molded product, and plays a major role in determining the quality and cost of production. It’s a complex process that requires high-quality materials and expert engineering. Injection molding tooling costs are based on the complexity of the mold, the material used, the number of cavities, the size of the cavity, and the level of quality required.
To make the best decision for your project, you must consider all the factors that impact cost. For example, a production volume with a large annual usage may demand a durable material like hardened steel, while lower-volume projects can benefit from less expensive options like aluminum and pre-hardened steel. Depending on the application, you may also need to select a tooling metal with specific properties like thermal conductivity or surface finish requirements.
Once the tools are ready, they’re put into a production line and closely monitored to identify and correct any issues that could affect part quality. Common problems include flash formation and warping, which can occur from too much pressure or misaligned mold parts. These issues can be addressed by adjusting pressure and ensuring proper alignment.
To prevent damage to the molded plastic, it’s critical that the injection mould tooling has an ejection mechanism that works smoothly. This is accomplished by creating a texture on the tooling surfaces that makes it easy for the molten plastic to release from the mold without damaging the finished product. The texture can be produced by CNC machining, grinding, EDM, turning, and more. The result is a smooth surface that looks great and offers durability. This is one area where you’ll want to work with an experienced manufacturer.
Design
The design phase is a critical one in the development of injection molding tools. It sets the stage for achieving accurate and reliable production of plastic parts. The key to successful tooling is to balance cost with the ability to meet production requirements. This is achieved by optimizing processes, utilizing efficient design techniques and selecting appropriate materials for the job.
The mold cavity is the heart of an injection molded part, and directly influences part quality, precision and finish. Proper cavity design can help reduce defects such as short shots, warping, sink marks and other surface irregularities. The use of proper runners and gating also significantly impacts production rates. Choosing the optimum material for strength, durability and finish can also lift part quality while providing cost benefits.
Runners are channels bored into the stationary mold half that direct melted plastic toward the core and cavity. They are designed to be narrower than the cavity and core to prevent a part from sticking to the walls of the mold, and to allow easy removal during the cooling process. The placement and diameter of gates can also impact production efficiency and the appearance of a finished product. Gates are typically placed in locations that can be easily accessed during the injection molding process.
A pickout is an insert that can be machined separately from the rest of the tool and placed in a mold before it is injected. This is used to achieve undercuts on interior surfaces. Using a pickout is more costly than using sliding shutoffs or side-action cores, but can be more effective. This method also requires that the core be strong enough to handle ejection and have a smooth surface so that it doesn’t detract from the overall appearance of a final plastic part.
Fabrication
After the initial design and prototyping are complete, fabrication of the injection mold tool begins. CNC machining is the primary technique, as it allows for precise shaping of individual mold components from raw materials such as steel and aluminum. Once fabricated, the various components are assembled into a complete mold. This phase involves meticulous attention to detail to ensure the assembled mold will perform as intended.
The choice of material for the mold is an important decision as it influences both the durability and quality of the resulting parts. Different thermoplastics have varying flow properties, shrink rates and thermal characteristics that must be considered during the design process. High-volume production demands durable materials like hardened steel, whereas simpler designs can be produced with cost-effective materials like aluminum and pre-hardened steel.
Core pins are slender rod-like components that form internal features of molded parts such as holes, channels and internal cavities. They play an essential role in ensuring consistency and accuracy in the internal geometry of a part, which can impact both aesthetics and functionality. Core pins can be designed with a variety of diameters and shapes depending on the required application.
The cooling system in an injection mold is composed of a series of tunnels and hoses. They are filled with water from an external pump to cool the molten plastic as it moves through them. This ensures that the molten plastic is at the proper temperature for the molding process. If the cooling system is not optimized or improperly maintained, issues can arise such as short shots, warping and surface defects. Regular maintenance and adherence to recommended production conditions will prevent these issues and prolong the lifespan of the mold.
Testing
When a new injection mold tool is ready for production, it first goes through a series of inspections and evaluations. The purpose of this process is to mitigate risks before moving into higher volumes. The inspections and evaluations focus primarily on verifying the dimensional accuracy of the finished parts. These measurements are compared to the original specifications of the product, and any issues discovered during this phase must be resolved before production can continue.
After the dimensional inspection, the mold is subjected to a series of quality tests, including:
The stationary A-side or cavity half of the mold attaches to the injection molding machine. The moving B-side or core half opens and closes around the stationary A-side when molten plastic is injected. The core or cavities create the external geometry of the molded part, which may contain features such as ribs, bosses, logos, and cosmetic textures. The core or cavity can also include cooling lines, a network of channels that a coolant flows through to control the molding process and minimize cycle times. Injection molding tools also have a number of other mechanical components, including guide pins, which fit into holes in the stationary A-side to align the two halves of the mold. Injection molds also have sprue bushes, which direct melted plastic from the injection nozzle to the cavities. The design and placement of these runners and gates is important for optimizing material flow and preventing defects such as short shots. A final test is a pressure curve, which evaluates the level of pressure used during the injection and packing phases. This information can be used to make necessary adjustments to the injection molding machine and injection parameters.
Manufacturing
The production of a plastic injection mold involves a complex process that requires a great deal of time and skill. The efficiency of this process has a lot to do with the quality and cost of the finished part. The key factors to consider include avoiding design flaws, scheduling the production run with a realistic time frame in mind and ensuring the correct tooling is selected for the job.
Once the design is approved by both the design engineers and the toolmakers, the CNC milling process begins. This entails cutting out the negative of the mold from a block of material like steel or aluminum. Injection molding is a precision process that requires expert machining techniques and attention to detail. The quality of the finished tooling has a direct impact on how well a molded part runs and its ability to meet strict tolerances.
At this point in the process it’s important to determine if hard or soft tooling will be used. The type of tooling will impact how long the mold can last and the cost of a production run. Soft tools are best for prototyping and low-volume production runs. They’re also less expensive than hard tooling, which saves money in the long run.
The next step is to acquire the equipment and parts needed for production. This includes the injection molding machine, a delivery system (known as a runner), and a cooling chamber. The runner is a series of channels that guide/direct a “shot” of molten plastic resin from the tooling injection point (called a sprue bush) into the cavities of the mold. Runners can be hot or cold and are designed to ensure an even flow of the resin across all cavities in the mold.